Porosity in Welding: Identifying Common Issues and Implementing Best Practices for Avoidance
Porosity in welding is a pervasive concern that typically goes unnoticed until it triggers significant issues with the integrity of welds. This common flaw can jeopardize the strength and longevity of bonded frameworks, posing safety dangers and leading to expensive rework. By understanding the origin triggers of porosity and carrying out effective prevention techniques, welders can considerably improve the high quality and reliability of their welds. In this conversation, we will check out the key factors adding to porosity development, examine its damaging results on weld performance, and talk about the very best techniques that can be embraced to decrease porosity occurrence in welding procedures.
Usual Reasons For Porosity

Using unclean or wet filler products can introduce pollutants right into the weld, adding to porosity problems. To alleviate these usual causes of porosity, complete cleansing of base metals, appropriate protecting gas option, and adherence to optimal welding parameters are necessary practices in attaining high-quality, porosity-free welds.
Effect of Porosity on Weld Top Quality

The visibility of porosity in welding can dramatically endanger the architectural integrity and mechanical properties of welded joints. Porosity produces voids within the weld steel, compromising its overall stamina and load-bearing capability.
One of the key effects of porosity is a reduction in the weld's ductility and strength. Welds with high porosity levels tend to display lower effect stamina and lowered capability to deform plastically prior to fracturing. This can be especially concerning in applications where the welded components are subjected to dynamic or cyclic loading problems. Porosity can restrain the weld's ability to successfully send forces, leading to early weld failing and prospective safety threats in important frameworks. What is Porosity.
Finest Practices for Porosity Prevention
To improve the architectural stability and high quality of welded joints, what particular measures can be executed to reduce the occurrence of porosity during the welding procedure? Making use of the right welding method for the details material being bonded, such as adjusting the welding angle and weapon setting, can further stop porosity. Routine assessment of welds and immediate removal of any issues identified during the welding procedure are crucial methods to stop porosity and produce high-grade welds.
Significance of Correct Welding Methods
Carrying out proper welding techniques is paramount in making certain the structural honesty and quality of welded joints, building upon the foundation of reliable porosity prevention procedures. Extreme heat can lead to raised porosity due to the entrapment of gases in the weld swimming pool. In addition, using the ideal welding parameters, such as voltage, present, and take a trip rate, is crucial for attaining sound welds with minimal porosity.
Furthermore, the option of welding process, whether it be MIG, TIG, or stick welding, must align with the details demands of the project to make certain ideal results. Appropriate cleansing and preparation of the base steel, along with selecting best site the ideal filler product, are additionally essential components of proficient welding techniques. By adhering to these best practices, welders can reduce the risk of porosity formation and produce top quality, structurally sound welds.
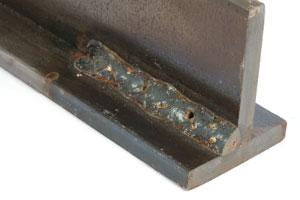
Examining and Quality Control Measures
Examining treatments are essential to spot and prevent porosity in welding, ensuring the toughness and resilience of the final product. Non-destructive screening methods such as ultrasonic testing, radiographic testing, and visual examination are frequently employed to identify prospective problems like porosity.
Carrying out pre-weld and post-weld inspections is likewise important in preserving quality control standards. Pre-weld assessments include verifying the materials, tools setups, and cleanliness of the workspace to avoid contamination. Post-weld assessments, on the various other hand, examine the final weld he said for any type of issues, including porosity, and validate that it meets specified criteria. Implementing a click for more info thorough top quality control plan that consists of detailed screening treatments and evaluations is paramount to reducing porosity problems and making certain the general quality of bonded joints.
Verdict
Finally, porosity in welding can be an usual concern that affects the top quality of welds. By identifying the common causes of porosity and carrying out finest techniques for prevention, such as proper welding strategies and testing steps, welders can guarantee high quality and trusted welds. It is important to prioritize prevention approaches to decrease the incident of porosity and maintain the stability of welded frameworks.
Comments on “What is Porosity in Welding: Usual Sources and Efficient Remedies”